{CANDELHOLDERS}
The objects are made to order. Contact me for price and shipping or delivery options. In Amman, you can purchase them directly from Rumman Collective shop.
This collection of stone candleholders is made of Ma’ani limestone. It started a series of interrogations, trials, and experiments as I worked with stone and stone artisans in a region where this material and practice are part of a rich cultural heritage. Stone buildings are ubiquitous in Palestine and Jordan. The industry for stone export ranges from statues and decorative objects to tiles cut for wall cladding.
Carving and shaping stone to a level where it becomes a thin layer changes its property and for this reason changes the type of objects it is possible to make with it. Slimming the mass to a thin layer makes it fragile. It is this specific layer that interests me. How can a material that is so robust, used on large scale buildings, become so vulnerable? How can its veins, the very reason it is so unique, also be the reason it breaks at the touch of a chisel or when mishandled?
Materials are part of our lives and even more so materials that are inherently connected to our landscape. We usually see (local) stone on large scale objects such as building facades or staircases. I was curious to see how it responds to smaller objects by seeing how the veins travel into the piece, making it unique and building a relationship with the viewer.
I started drawing a few pieces and used grid, shape, and function almost as excuses to return to the drawing board which I had given up for several years after I stopped practicing architecture. I tried several times; disregarded the first sketches, and drew others. I was attracted to extracting circular volumes from stone masses. I designed small functional objects, delicate pieces.
The first prototypes were made in a factory in Bethlehem. There was minimal conversation with the managers at the factory. They took the drawings and programmed their water jet machines to cut the pieces and hollowed them out by hand. They rushed to get this done between two big orders. They conveyed the shape I wanted, but it missed intricacy and detail. I am certain that we could have reached a good level of satisfaction with some additional patience and time. They ended up rejecting the project as it was too time consuming and required a great deal of patience. In parallel, I also worked with a turning workshop to produce the brass connector. We had numerous conversations about the way to make this joint, how it will carry the stone mass on top, and how it will rotate to make the collection dismantlable and interchangeable.
Following this first prototype, I faced months of challenges to find the right partner for this collection. I was looking for someone who would give me enough space to prototype this collection properly, and share our expertise together, but most importantly give the time and space needed for a design to reach its maturity. I contacted ten factories, artisans, and stone suppliers across Italy, Jordan, and Palestine to explore the production of the collection together. Although the designs appear simple at first glance, the intricate details are challenging to carve in this fragile material. Most of the suppliers either declined the project due to its complexity and low profitability, or quoted an exorbitant price.
After several design trials, the production of actual prototypes, and experimenting with function and materials, I opted for Jordanian limestone from Ma’an, known as Jazeera, for the striking patterns of its red and ochre veins. The region is home to a variety of stone quarries, each producing a distinct type of stone with its own unique characteristics and colors. Some of the most popular stones from Ma’an include travertine, limestone, and marble.
The collection is made of several hand-shaped stone masses connected by a brass piece. Its playfulness invites the user to make their own combination. The entire collection allows for a variety of different possibilities given by the three bases and six tops and can host three types of candles (tealight, tall, and pillar candles). Indeed, the endless possibilities that these materials and techniques have, gave the project complexity, and raised many questions as to when to stop, and how to stop, knowing that there is much more that can be added to each object.
-
Top 5 | suitable for tealight candles
-
Base 3 | ⌀: 8 cm; H: 8 cm
-
Top 2 | suitable for tall candles
⌀ candle: 2 cm
-
Base 1 | ⌀: 6 cm; H: 10 cm
-
Top 3 | suitable for pillar candles
⌀ candle: 7 cm
-
Base 1 | ⌀: 6 cm; H: 10 cm
-
Top 1 | suitable for tall candles
⌀ candle: 2 cm
-
Base 3 | ⌀: 8 cm; H: 8 cm
-
Top 4 | suitable for pillar candles
⌀ candle: 7 cm
-
Base 3 | ⌀: 8 cm; H: 8 cm
-
Top 6 | suitable for tealight candles
⌀ candle: 2 cm
-
Base 2 | ⌀: 7 cm; H: 6 cm
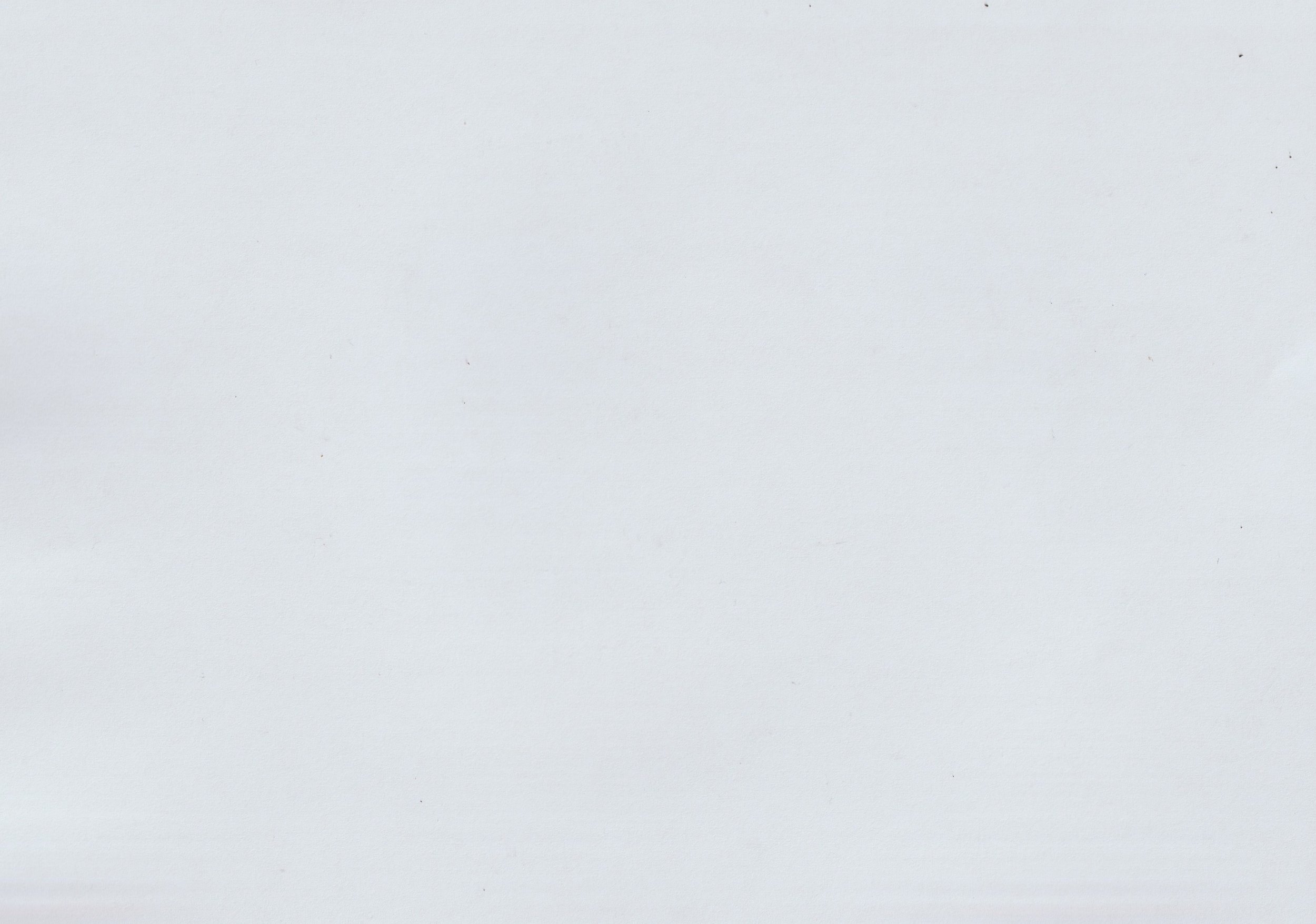
CARE FOR YOUR OBJECTS
The stone pieces you have are fragile objects. Always carry the object from the base.
Be gentle while rotating the stone onto the metal, do not use force. In the case the metal connector is stuck onto the stone, tap gently to disconnect, or use a pincer onto the metal dents, not on the plain surface to avoid scratching it.
The metal connector will tarnish with time as it does not have any varnish.
Clean stone and metal pieces with a soft damp cloth.

TOP 1
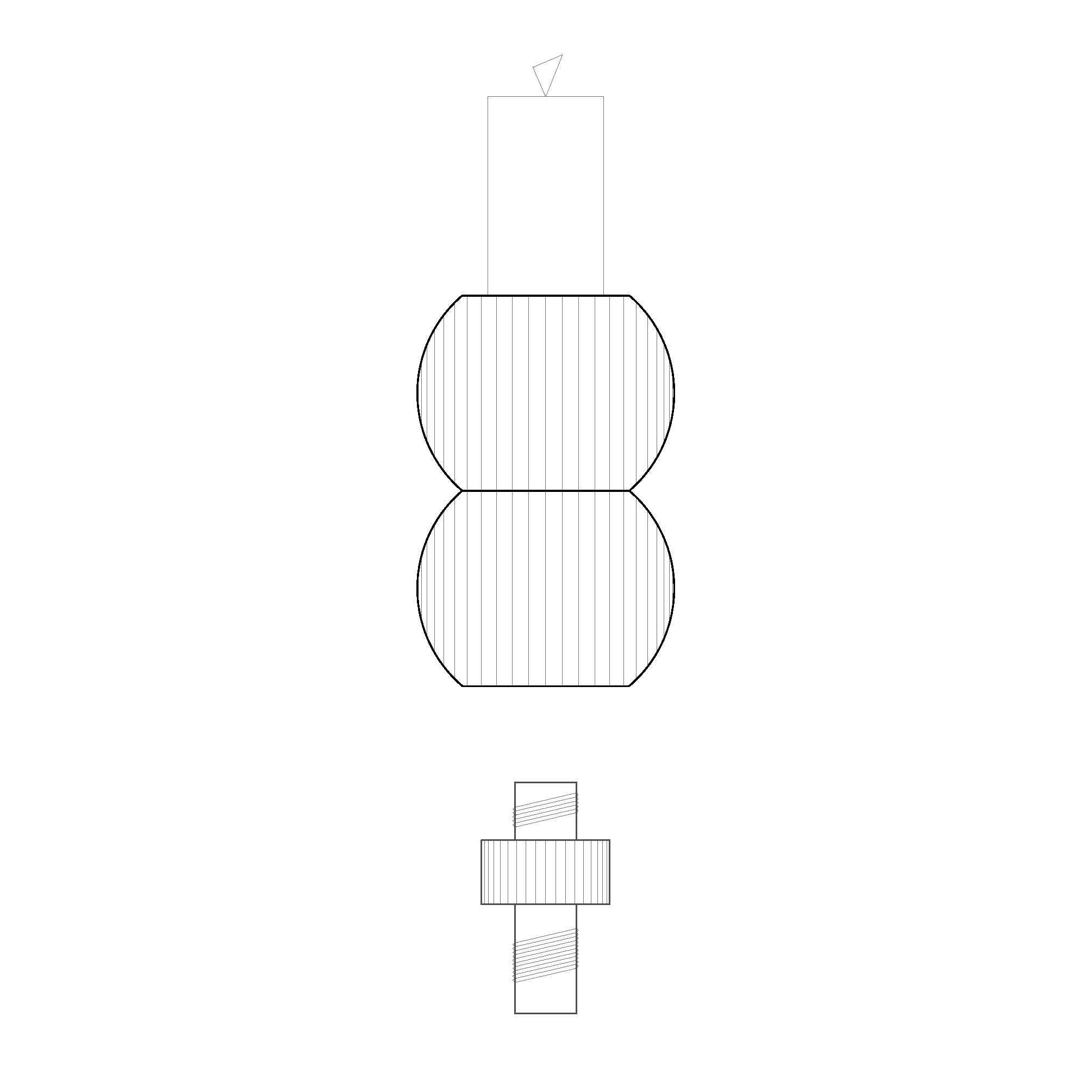
TOP 2

TOP 3

TOP 4

TOP 5
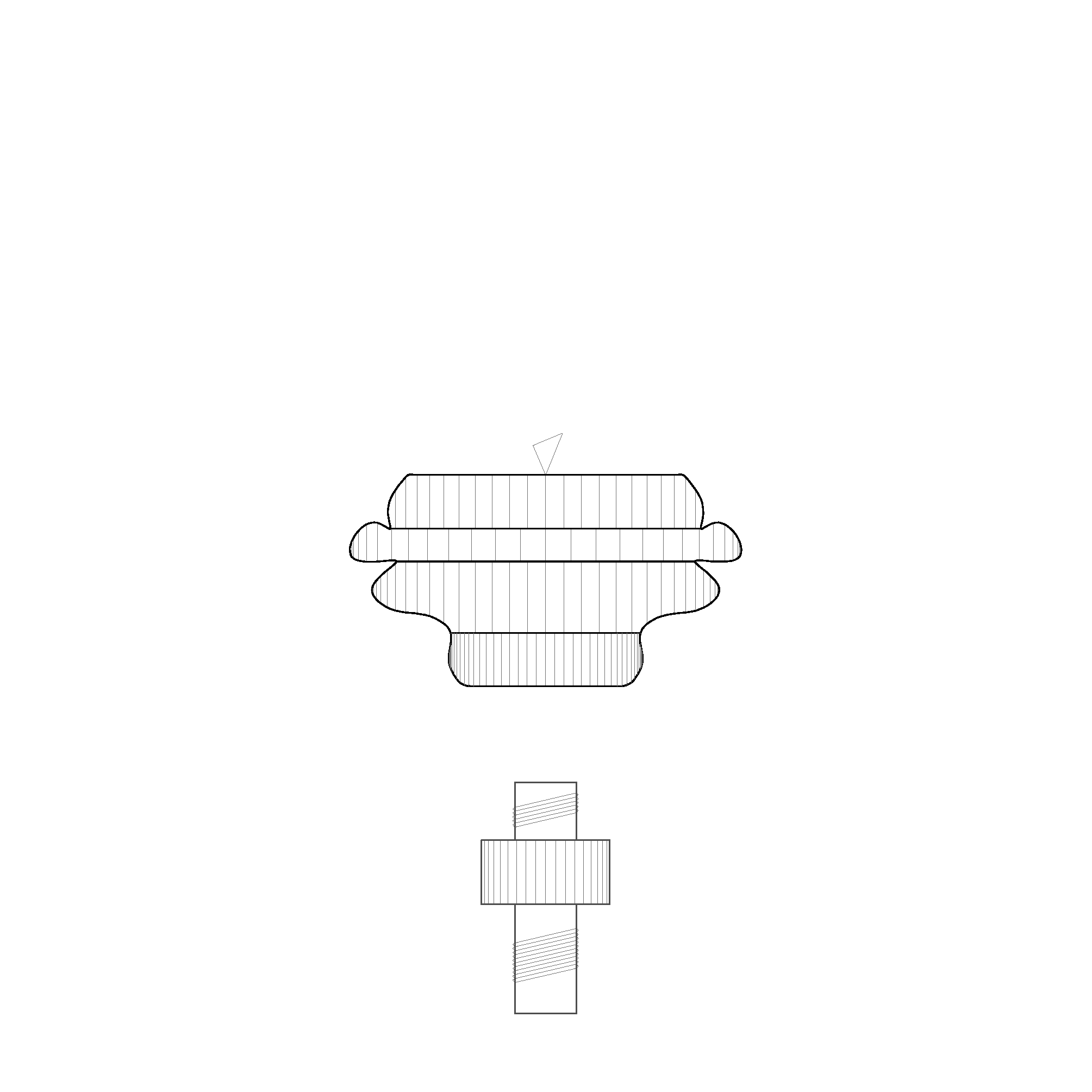
TOP 6
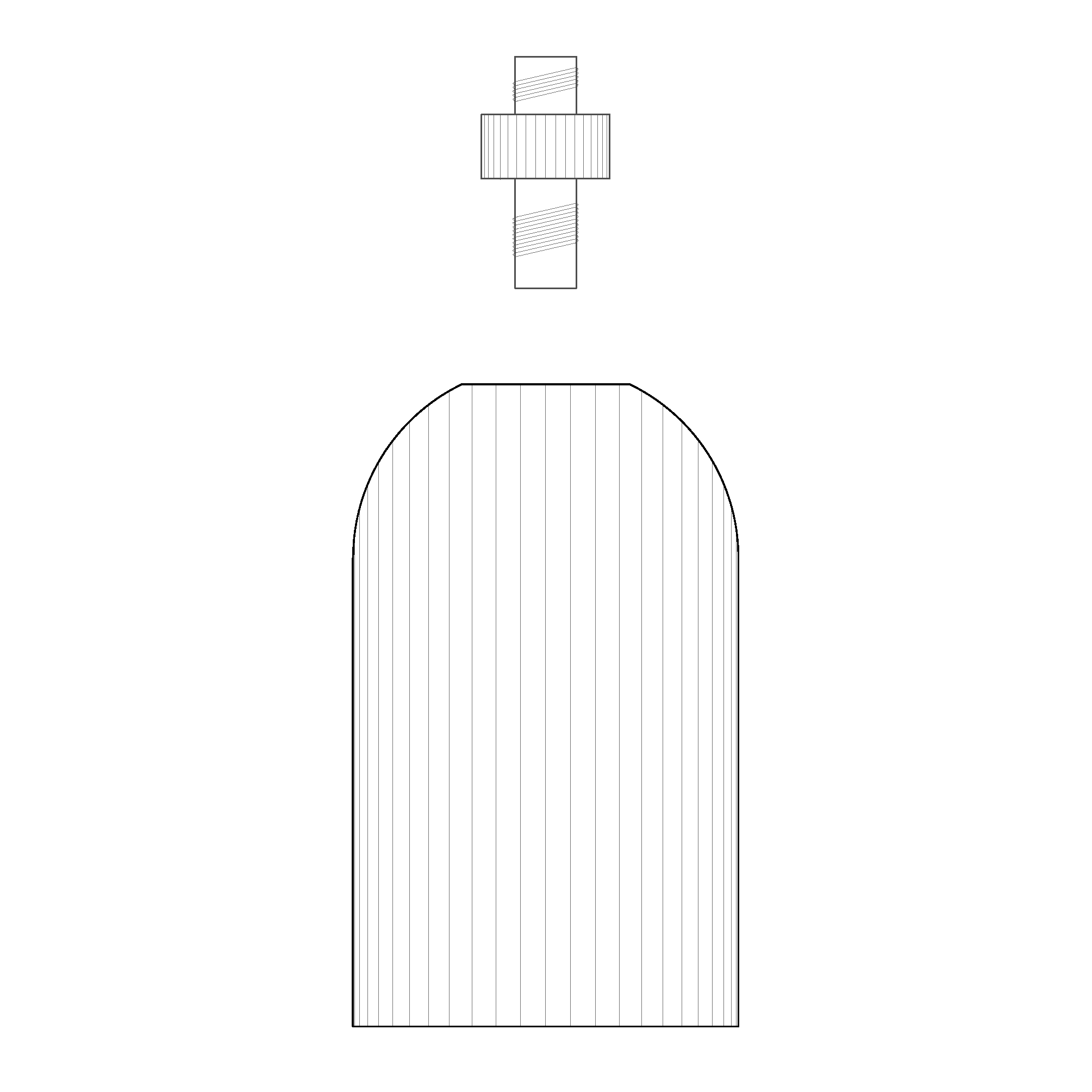
BASE 1

BASE 2

BASE 3
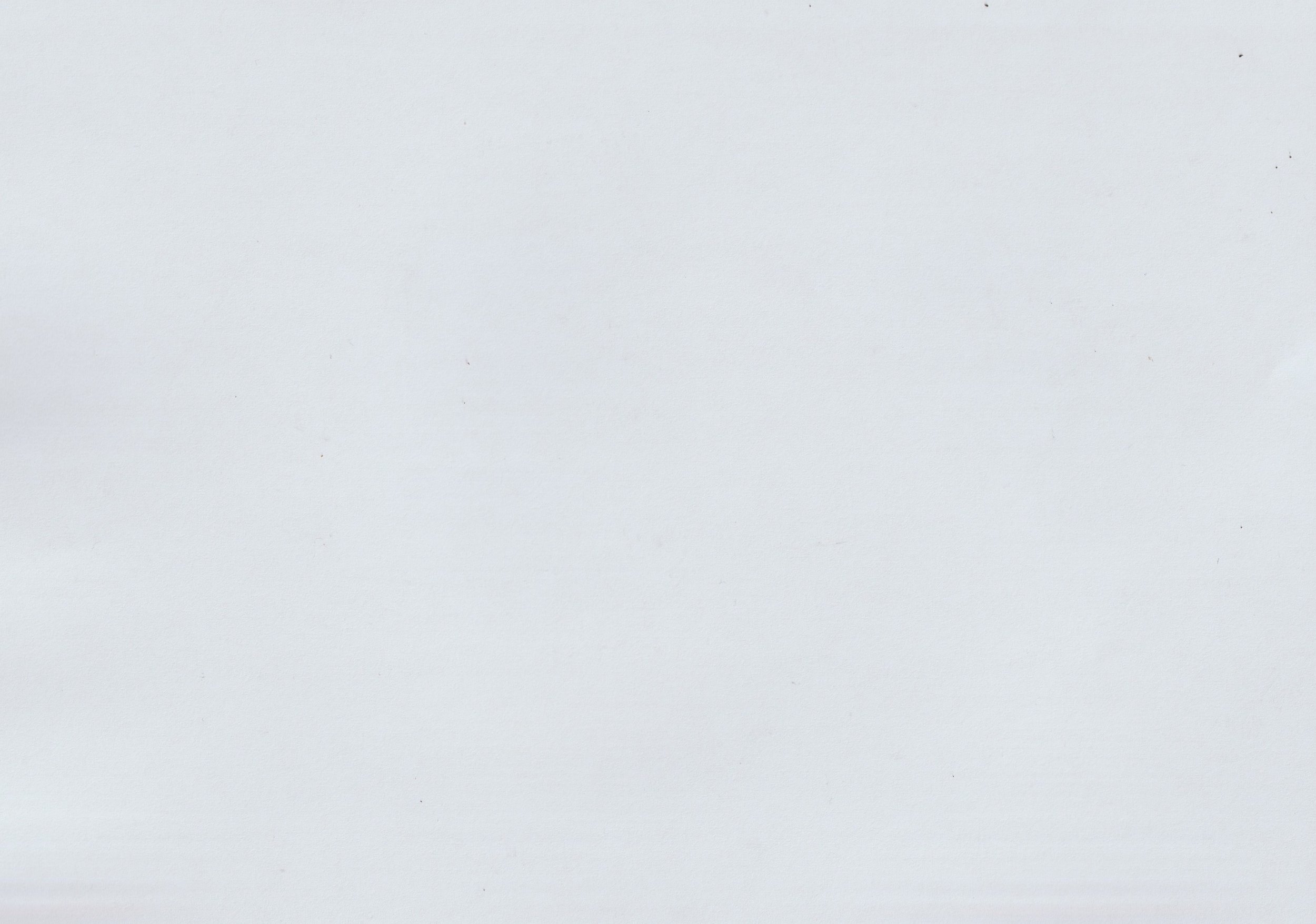
MATERIALS
The stone objects are made with Ma’ani limestone. The metal connector is made of brass rods, unvarnished, they will tarnish.
I collaborated with Abu Ahmad, a stone carver in Amman who originally comes from Artas, a village near Bethlehem. He acquired his stone carving skills through self-guided learning after working on construction sites in Jordan. Based in his home workshop in Amman, surrounded by crops and a small farm, his workshop overlooks the region of Salt. The valley is especially lush and green in spring. Abu Ahmad makes crafted stone pieces using a variety of local and imported raw materials. Each project is a learning experience for him, in which he is deeply immersed in perfecting every detail. He relies on handheld machines and small tools to bring his projects to fruition.
In the realm of metalwork, my long-time collaborator Mustafa joined forces with me. We had worked together for several years and I had already spent much time in his workshop, exploring materials and drawing inspiration from his expertise. For this project, we designed and produced multiple versions of the metal connector, experimenting with aluminum, brass, and copper, using different heights and textures. This approach pushed the playfulness of this collection. However, we ultimately opted for a unique brass connector that emphasized the two stone pieces above and below it.
This collection raised many challenges and a series of interrogations in terms of local production. It required a great deal of patience and a strong belief that it was possible to produce locally. By cultivating robust and trustworthy relationships with artisans, the process becomes more manageable. With mutual understanding and adaptation to production constraints, we can proactively seek solutions to overcome these challenges.
Photos by Hussam Hasan, 2024